Lumi cords manufacturer: cords that make a difference
In mass production, even the smallest component can affect overall efficiency. Technical cords and ropes, though often invisible to the end user, are essential construction, fastening, or decorative elements in many industries. In furniture, toys, outdoor equipment, or automotive accessories, a properly matched cord is key—especially where automation, assembly speed, and repeatability are crucial. More companies are choosing custom-made cords and ropes over generic warehouse options, which often fail to meet technical requirements.

Industrial use of technical cords
Technical cords are used in various industries, especially furniture, outdoor gear, and toy manufacturing. In furniture production, they play a crucial role in upholstered constructions, including backrests, headrests, or folding systems. In outdoor applications, cords are used in tents, tarps, and backpacks, requiring resistance to stretch, moisture, and UV rays.
A rapidly growing area is the toy industry, where cords are used for interactive elements, sensory bags, or educational toys. In these cases, technical properties are important—but so are safety certifications, material quality, and smooth finishing.
The problem with standard cords
Producers using stock cords quickly face limitations. Off-the-shelf options may be the wrong length, too stiff, or mismatched in color. Even worse, they often come with unsecured ends, which need manual trimming, sealing, or sewing—slowing down production and increasing costs. Instead of helping the process, these cords become a bottleneck. In mass production, every second counts, and deviations can cause errors, delays, and complaints.
What does a custom cord order include?
A custom-made cord means adapting the product to the specific production line—both technically and visually. Clients can choose the material (e.g., polypropylene, polyester, cotton, TWARON), diameter, braid type, core, and color. Cords can be delivered loose in cardboard boxes or on spools, with customizable spool length.
Cords can also be cut to exact lengths and finished with heat sealing or plastic/metal tips. Personalization also includes brand color matching and the option to add product labels or branding. This flexibility results in a component that meets technical needs without extra finishing or adjustments during assembly.
Real benefits for mass production
Custom cords help speed up assembly, reduce errors, and minimize material and time waste. The component arrives ready to use—no extra steps required. This makes the process more repeatable, easier to automate, and less prone to error. The entire supply chain—from order to delivery—becomes more predictable. And the final product quality improves, which enhances the brand’s perception.
Case study: faster production in the toy industry
One of our clients—a manufacturer of educational and sensory toys—initially used bulk cords that required trimming and finishing during assembly. This was time-consuming and wasteful. After switching to custom-made cords—pre-cut, colorful, with safe finishes—assembly time dropped by 20%. The client improved production efficiency and achieved better product consistency and appearance, leading to more positive market feedback.
How the collaboration works
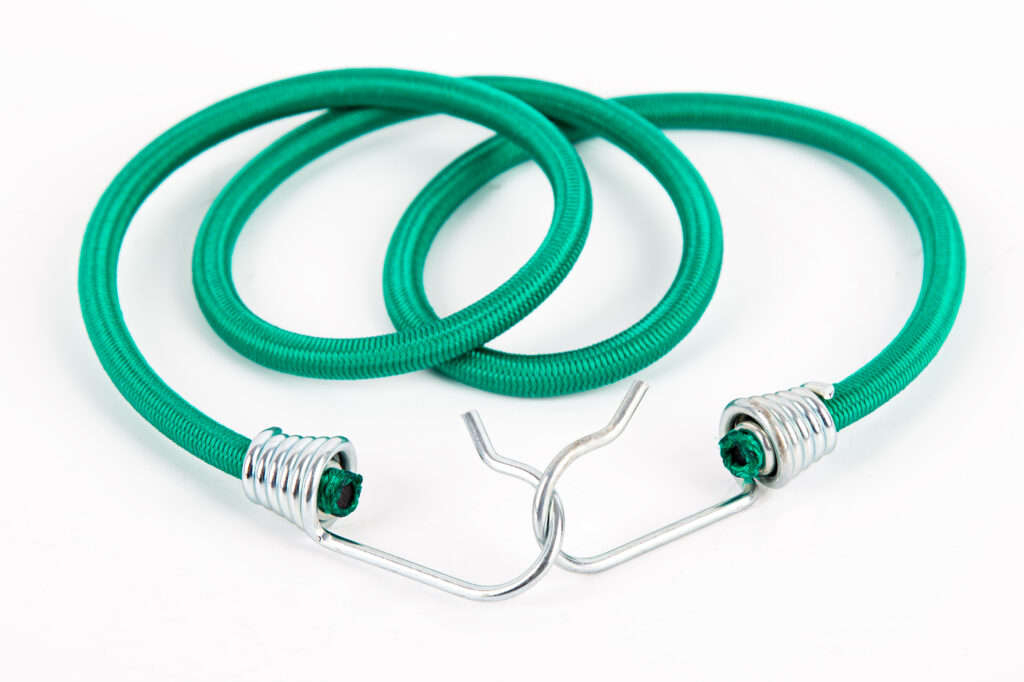
Everything starts with a conversation—understanding the client’s needs and production of ropes and cords specifics. Based on that, we propose the best technical and material solution and prepare samples. Once tested in real production conditions, we move to serial manufacturing. Orders are handled flexibly, with adjustable parameters and full quality control. This approach ensures a perfect match for the production line and quick adjustments when needed.
Summary: small component, big savings
Cords may seem like a minor detail, but they often determine whether production runs smoothly or causes extra costs. Custom-made cords, ropes, and bungee cords are increasingly chosen by manufacturers who value quality, efficiency, and consistency. A tailored component from an experienced producer becomes more than just a part—it’s a tool for optimizing your entire production process. Do you want to see how custom cords can improve your production line?
Get in touch—we’ll create a solution tailored to your needs and industry requirements.